EBOOK - The Mechanical Design Process (David G.Ullman)
I have been a designer all my life. I have designed bicycles, medical equipment, furniture, and sculpture, both static and dynamic. Designing objects has come easy for me. I have been fortunate in having whatever talents are necessary to be a successful designer.
However, after a number of years of teaching mechanical design courses, I came to the realization that I didn’t know how to teach what I knew so well. I could show students examples of good-quality design and poorquality design. I could give them case histories of designers in action. I could suggest design ideas. But I could not tell them what to do to solve a design problem.
Additionally, I realized from talking with other mechanical design teachers that I was not alone.
This situation reminded me of an experience I had once had on ice skates. As a novice skater I could stand up and go forward, lamely.
A friend (a teacher by trade) could easily skate forward and backward as well. He had been skating since he was a young boy, and it was second nature to him. One day while we were skating together, I asked him to teach me how to skate backward. He said it was easy, told me to watch, and skated off backward. But when I tried to do what he did, I immediately fell down. As he helped me up, I asked him to tell me exactly what to do, not just show me. After a moment’s thought, he concluded that he couldn’t actually describe the feat to me.
I still can’t skate backward, and I suppose he still can’t explain the skills involved in skating backward. The frustration that I felt falling down as my friend skated with ease must have been the same emotion felt by my design students when I failed to tell them exactly what to do to solve a design problem.
This realization led me to study the process of mechanical design, and it eventually led to this book. Part has been original research, part studying U.S. industry, part studying foreign design techniques, and part trying different teaching approaches on design classes. I came to four basic conclusions about mechanical design as a result of these studies:
1. The only way to learn about design is to do design.
2. In engineering design, the designer uses three types of knowledge: knowledge to generate ideas, knowledge to evaluate ideas and make decisions, and knowledge to structure the design process. Idea generation comes from experience and natural ability. Idea evaluation comes partially from experience and partially from formal training, and is the focus of most engineering education. Generative and evaluative knowledge are forms of domain-specific knowledge. Knowledge about the design process and decision making is largely independent of domain-specific knowledge.
3. A design process that results in a quality product can be learned, provided there is enough ability and experience to generate ideas and enough experience and training to evaluate them.
4. A design process should be learned in a dual setting: in an academic environment and, at the same time, in an environment that simulates industrial realities.
CHAPTER1 Why Study the Design Process1
1.1 Introduction 1
1.2 Measuring the Design Process with Product
Cost, Quality, and Time to Market 3
1.3 The History of the Design Process 8
1.4 The Life of a Product 10
1.5 The Many Solutions for Design
Problems 15
1.6 The Basic Actions of Problem Solving 17
1.7 Knowledge and Learning During Design 19
1.8 Design for Sustainability 20
1.9 Summary 21
1.10 Sources 22
1.11 Exercises 22
CHAPTER2 Understanding Mechanical Design 25
2.1 Introduction 25
2.2 Importance of Product Function, Behavior,
and Performance 28
2.3 Mechanical Design Languages
and Abstraction 30
2.4 Different Types of Mechanical
Design Problems 33
2.5 Constraints, Goals, and
Design Decisions 40
2.6 Product Decomposition 41
2.7 Summary 44
2.8 Sources 44
2.9 Exercises 45
2.10 On the Web 45
CHAPTER3 Designers and Design Teams 47
3.1 Introduction 47
3.2 The Individual Designer: A Model of Human
Information Processing 48
3.3 Mental Processes That Occur
During Design 56
3.4 Characteristics of Creators 64
3.5 The Structure of Design Teams 66
3.6 Building Design Team Performance 72
3.7 Summary 78
3.8 Sources 78
3.9 Exercises 79
3.10 On the Web 80
CHAPTER4 The Design Process and Product Discovery 81
4.1 Introduction 81
4.2 Overview of the Design Process 81
4.3 Designing Quality into Products 92
4.4 Product Discovery 95
4.5 Choosing a Project 101
4.6 Summary 109
4.7 Sources 110
4.8 Exercises 110
4.9 On the Web 110
CHAPTER5 Planning for Design 111
5.1 Introduction 111
5.2 Types of Project Plans 113
5.3 Planning for Deliverables—
The Development of Information 117
5.4 Building a Plan 126
5.5 Design Plan Examples 134
5.6 Communication During the
Design Process 137
5.7 Summary 141
5.8 Sources 141
5.9 Exercises 142
5.10 On the Web 142
CHAPTER6 Understanding the Problem and the Development of Engineering
Specifications 143
6.1 Introduction 143
6.2 Step 1: Identify the Customers:
Who Are They? 151
6.3 Step 2: Determine the Customers’
Requirements:WhatDo the Customers Want? 151
6.4 Step 3: Determine Relative Importance of the
Requirements:Who Versus What 155
6.5 Step 4: Identify and Evaluate the Competition:
How Satisfied Are the CustomersNow? 157
6.6 Step 5: Generate Engineering
Specifications:HowWill the Customers’
Requirement Be Met? 158
6.7 Step 6: Relate Customers’ Requirements to
Engineering Specifications:Howto Measure What? 163
6.8 Step 7: Set Engineering Specification Targets
and Importance:HowMuch Is Good Enough? 164
6.9 Step 8: Identify Relationships Between
Engineering Specifications: How Are the
HowsDependent on Each Other? 166
6.10 Further Comments on QFD 168
6.11 Summary 169
6.12 Sources 169
6.13 Exercises 169
6.14 On the Web 170
CHAPTER7 Concept Generation 171
7.1 Introduction 171
7.2 Understanding the Function of Existing
Devices 176
7.3 ATechnique for Designing with Function 181
7.4 Basic Methods of Generating Concepts 189
7.5 Patents as a Source of Ideas 194
7.6 Using Contradictions to Generate Ideas 197
7.7 The Theory of Inventive Machines, TRIZ 201
7.8 Building a Morphology 204
7.9 Other Important Concerns During Concept
Generation 208
7.10 Summary 209
7.11 Sources 209
7.12 Exercises 211
7.13 On the Web 211
CHAPTER8 Concept Evaluation and Selection 213
8.1 Introduction 213
8.2 Concept Evaluation Information 215
8.3 Feasibility Evaluations 218
8.4 Technology Readiness 219
8.5 The Decision Matrix—Pugh’s Method 221
8.6 Product, Project, and Decision Risk 226
Contents ix
8.7 Robust Decision Making 233
8.8 Summary 239
8.9 Sources 239
8.10 Exercises 240
8.11 On the Web 240
CHAPTER9 Product Generation 241
9.1 Introduction 241
9.2 BOMs 245
9.3 Form Generation 246
9.4 Materials and Process Selection 264
9.5 Vendor Development 266
9.6 Generating a Suspension Design for the
Marin 2008 Mount Vision Pro Bicycle 269
9.7 Summary 276
9.8 Sources 276
9.9 Exercises 277
9.10 On the Web 278
CHAPTER10 Product Evaluation for Performance and the Effects
of Variation 279
10.1 Introduction 279
10.2 Monitoring Functional Change 280
10.3 The Goals of Performance Evaluation 281
10.4 Trade-Off Management 284
10.5 Accuracy, Variation, and Noise 286
10.6 Modeling for Performance Evaluation 292
10.7 Tolerance Analysis 296
10.8 Sensitivity Analysis 302
10.9 Robust Design by Analysis 305
10.10 Robust Design Through Testing 308
10.11 Summary 313
10.12 Sources 313
10.13 Exercises 314
CHAPTER11 Product Evaluation: Design For Cost, Manufacture, Assembly,
and Other Measures 315
11.1 Introduction 315
11.2 DFC—Design For Cost 315
11.3 DFV—Design For Value 325
11.4 DFM—Design For Manufacture 328
11.5 DFA—Design-For-Assembly
Evaluation 329
11.6 DFR—Design For Reliability 350
11.7 DFT and DFM—Design For Test and
Maintenance 357
11.8 DFE—Design For the Environment 358
11.9 Summary 360
11.10 Sources 361
11.11 Exercises 361
11.12 On the Web 362
CHAPTER12 Wrapping Up the Design Process and Supporting the Product 363
12.1 Introduction 363
12.2 Design Documentation and
Communication 366
12.3 Support 368
12.4 Engineering Changes 370
12.5 Patent Applications 371
12.6 Design for End of Life 375
12.7 Sources 378
12.8 On the Web 378
Properties of 25 Materials Most Commonly Used in Mechanical
Design 379
A.1 Introduction 379
A.2 Properties of the Most Commonly Used Materials 380
A.3 Materials Used in Common Items 393
A.4 Sources 394
Normal Probability 397
B.1 Introduction 397
B.2 Other Measures 401
The Factor of Safety as a Design Variable 403
C.1 Introduction 403
C.2 The Classical Rule-of-Thumb Factor
of Safety 405
C.3 The Statistical, Reliability-Based,
Factor of Safety 406
C.4 Sources 414
Human Factors in Design 415
D.1 Introduction 415
D.2 The Human in the Workspace 416
D.3 The Human as Source of Power 419
D.4 The Human as Sensor and
Controller 419
D.5 Sources 426
Index 427
LINK DOWNLOAD
I have been a designer all my life. I have designed bicycles, medical equipment, furniture, and sculpture, both static and dynamic. Designing objects has come easy for me. I have been fortunate in having whatever talents are necessary to be a successful designer.
However, after a number of years of teaching mechanical design courses, I came to the realization that I didn’t know how to teach what I knew so well. I could show students examples of good-quality design and poorquality design. I could give them case histories of designers in action. I could suggest design ideas. But I could not tell them what to do to solve a design problem.
Additionally, I realized from talking with other mechanical design teachers that I was not alone.
This situation reminded me of an experience I had once had on ice skates. As a novice skater I could stand up and go forward, lamely.
A friend (a teacher by trade) could easily skate forward and backward as well. He had been skating since he was a young boy, and it was second nature to him. One day while we were skating together, I asked him to teach me how to skate backward. He said it was easy, told me to watch, and skated off backward. But when I tried to do what he did, I immediately fell down. As he helped me up, I asked him to tell me exactly what to do, not just show me. After a moment’s thought, he concluded that he couldn’t actually describe the feat to me.
I still can’t skate backward, and I suppose he still can’t explain the skills involved in skating backward. The frustration that I felt falling down as my friend skated with ease must have been the same emotion felt by my design students when I failed to tell them exactly what to do to solve a design problem.
This realization led me to study the process of mechanical design, and it eventually led to this book. Part has been original research, part studying U.S. industry, part studying foreign design techniques, and part trying different teaching approaches on design classes. I came to four basic conclusions about mechanical design as a result of these studies:
1. The only way to learn about design is to do design.
2. In engineering design, the designer uses three types of knowledge: knowledge to generate ideas, knowledge to evaluate ideas and make decisions, and knowledge to structure the design process. Idea generation comes from experience and natural ability. Idea evaluation comes partially from experience and partially from formal training, and is the focus of most engineering education. Generative and evaluative knowledge are forms of domain-specific knowledge. Knowledge about the design process and decision making is largely independent of domain-specific knowledge.
3. A design process that results in a quality product can be learned, provided there is enough ability and experience to generate ideas and enough experience and training to evaluate them.
4. A design process should be learned in a dual setting: in an academic environment and, at the same time, in an environment that simulates industrial realities.
CHAPTER1 Why Study the Design Process1
1.1 Introduction 1
1.2 Measuring the Design Process with Product
Cost, Quality, and Time to Market 3
1.3 The History of the Design Process 8
1.4 The Life of a Product 10
1.5 The Many Solutions for Design
Problems 15
1.6 The Basic Actions of Problem Solving 17
1.7 Knowledge and Learning During Design 19
1.8 Design for Sustainability 20
1.9 Summary 21
1.10 Sources 22
1.11 Exercises 22
CHAPTER2 Understanding Mechanical Design 25
2.1 Introduction 25
2.2 Importance of Product Function, Behavior,
and Performance 28
2.3 Mechanical Design Languages
and Abstraction 30
2.4 Different Types of Mechanical
Design Problems 33
2.5 Constraints, Goals, and
Design Decisions 40
2.6 Product Decomposition 41
2.7 Summary 44
2.8 Sources 44
2.9 Exercises 45
2.10 On the Web 45
CHAPTER3 Designers and Design Teams 47
3.1 Introduction 47
3.2 The Individual Designer: A Model of Human
Information Processing 48
3.3 Mental Processes That Occur
During Design 56
3.4 Characteristics of Creators 64
3.5 The Structure of Design Teams 66
3.6 Building Design Team Performance 72
3.7 Summary 78
3.8 Sources 78
3.9 Exercises 79
3.10 On the Web 80
CHAPTER4 The Design Process and Product Discovery 81
4.1 Introduction 81
4.2 Overview of the Design Process 81
4.3 Designing Quality into Products 92
4.4 Product Discovery 95
4.5 Choosing a Project 101
4.6 Summary 109
4.7 Sources 110
4.8 Exercises 110
4.9 On the Web 110
CHAPTER5 Planning for Design 111
5.1 Introduction 111
5.2 Types of Project Plans 113
5.3 Planning for Deliverables—
The Development of Information 117
5.4 Building a Plan 126
5.5 Design Plan Examples 134
5.6 Communication During the
Design Process 137
5.7 Summary 141
5.8 Sources 141
5.9 Exercises 142
5.10 On the Web 142
CHAPTER6 Understanding the Problem and the Development of Engineering
Specifications 143
6.1 Introduction 143
6.2 Step 1: Identify the Customers:
Who Are They? 151
6.3 Step 2: Determine the Customers’
Requirements:WhatDo the Customers Want? 151
6.4 Step 3: Determine Relative Importance of the
Requirements:Who Versus What 155
6.5 Step 4: Identify and Evaluate the Competition:
How Satisfied Are the CustomersNow? 157
6.6 Step 5: Generate Engineering
Specifications:HowWill the Customers’
Requirement Be Met? 158
6.7 Step 6: Relate Customers’ Requirements to
Engineering Specifications:Howto Measure What? 163
6.8 Step 7: Set Engineering Specification Targets
and Importance:HowMuch Is Good Enough? 164
6.9 Step 8: Identify Relationships Between
Engineering Specifications: How Are the
HowsDependent on Each Other? 166
6.10 Further Comments on QFD 168
6.11 Summary 169
6.12 Sources 169
6.13 Exercises 169
6.14 On the Web 170
CHAPTER7 Concept Generation 171
7.1 Introduction 171
7.2 Understanding the Function of Existing
Devices 176
7.3 ATechnique for Designing with Function 181
7.4 Basic Methods of Generating Concepts 189
7.5 Patents as a Source of Ideas 194
7.6 Using Contradictions to Generate Ideas 197
7.7 The Theory of Inventive Machines, TRIZ 201
7.8 Building a Morphology 204
7.9 Other Important Concerns During Concept
Generation 208
7.10 Summary 209
7.11 Sources 209
7.12 Exercises 211
7.13 On the Web 211
CHAPTER8 Concept Evaluation and Selection 213
8.1 Introduction 213
8.2 Concept Evaluation Information 215
8.3 Feasibility Evaluations 218
8.4 Technology Readiness 219
8.5 The Decision Matrix—Pugh’s Method 221
8.6 Product, Project, and Decision Risk 226
Contents ix
8.7 Robust Decision Making 233
8.8 Summary 239
8.9 Sources 239
8.10 Exercises 240
8.11 On the Web 240
CHAPTER9 Product Generation 241
9.1 Introduction 241
9.2 BOMs 245
9.3 Form Generation 246
9.4 Materials and Process Selection 264
9.5 Vendor Development 266
9.6 Generating a Suspension Design for the
Marin 2008 Mount Vision Pro Bicycle 269
9.7 Summary 276
9.8 Sources 276
9.9 Exercises 277
9.10 On the Web 278
CHAPTER10 Product Evaluation for Performance and the Effects
of Variation 279
10.1 Introduction 279
10.2 Monitoring Functional Change 280
10.3 The Goals of Performance Evaluation 281
10.4 Trade-Off Management 284
10.5 Accuracy, Variation, and Noise 286
10.6 Modeling for Performance Evaluation 292
10.7 Tolerance Analysis 296
10.8 Sensitivity Analysis 302
10.9 Robust Design by Analysis 305
10.10 Robust Design Through Testing 308
10.11 Summary 313
10.12 Sources 313
10.13 Exercises 314
CHAPTER11 Product Evaluation: Design For Cost, Manufacture, Assembly,
and Other Measures 315
11.1 Introduction 315
11.2 DFC—Design For Cost 315
11.3 DFV—Design For Value 325
11.4 DFM—Design For Manufacture 328
11.5 DFA—Design-For-Assembly
Evaluation 329
11.6 DFR—Design For Reliability 350
11.7 DFT and DFM—Design For Test and
Maintenance 357
11.8 DFE—Design For the Environment 358
11.9 Summary 360
11.10 Sources 361
11.11 Exercises 361
11.12 On the Web 362
CHAPTER12 Wrapping Up the Design Process and Supporting the Product 363
12.1 Introduction 363
12.2 Design Documentation and
Communication 366
12.3 Support 368
12.4 Engineering Changes 370
12.5 Patent Applications 371
12.6 Design for End of Life 375
12.7 Sources 378
12.8 On the Web 378
Properties of 25 Materials Most Commonly Used in Mechanical
Design 379
A.1 Introduction 379
A.2 Properties of the Most Commonly Used Materials 380
A.3 Materials Used in Common Items 393
A.4 Sources 394
Normal Probability 397
B.1 Introduction 397
B.2 Other Measures 401
The Factor of Safety as a Design Variable 403
C.1 Introduction 403
C.2 The Classical Rule-of-Thumb Factor
of Safety 405
C.3 The Statistical, Reliability-Based,
Factor of Safety 406
C.4 Sources 414
Human Factors in Design 415
D.1 Introduction 415
D.2 The Human in the Workspace 416
D.3 The Human as Source of Power 419
D.4 The Human as Sensor and
Controller 419
D.5 Sources 426
Index 427
LINK DOWNLOAD

%20(1).png)
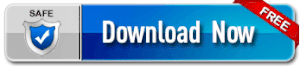
.png)
Không có nhận xét nào: